The Vital Role of Sodium Hypochlorite Placard in Industrial Safety Measures
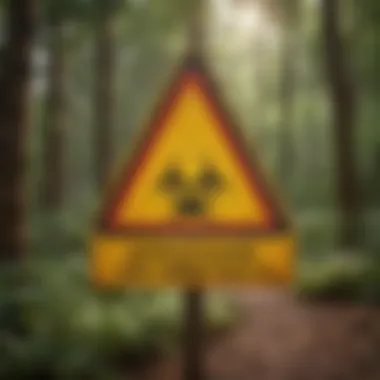
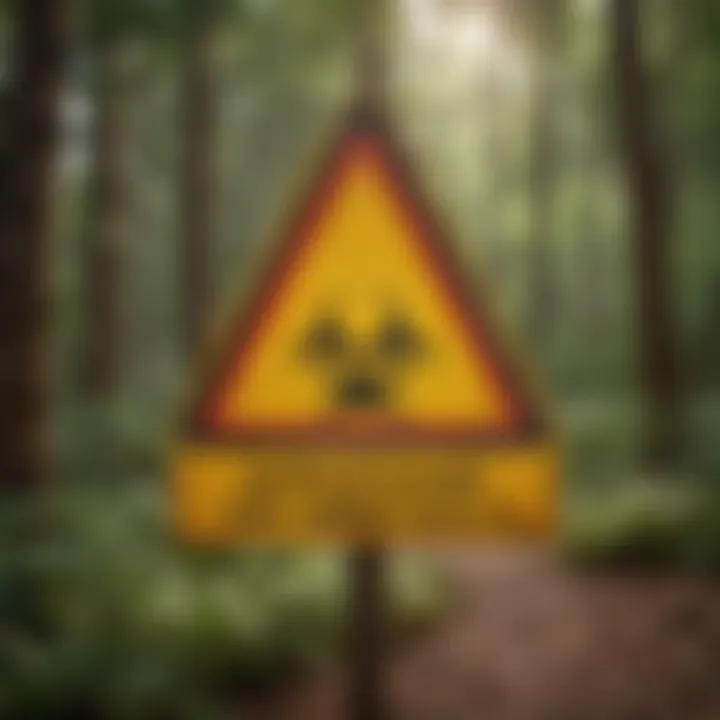
Industrial safety relies heavily on the effective communication of potential hazards, and one critical element in this communication chain is the sodium hypochlorite placard. A sodium hypochlorite placard serves as a warning sign, alerting workers and the public to the presence of this hazardous chemical. In the sections below, we will explore the composition of the placard, its regulatory requirements, and its pivotal role in safeguarding individuals from the dangers associated with sodium hypochlorite.
Sodium Hypochlorite Placard Overview
Before delving into the specifics of sodium hypochlorite placards, it is essential to understand the composition and design of these crucial safety markers. The placard typically features a distinct color scheme and symbol that indicate the presence of sodium hypochlorite. Regulatory authorities mandate the consistent display of these placards in areas where the chemical is stored or used, ensuring visibility and awareness among all personnel.
Regulatory Compliance and Safety Standards
Compliance with regulatory standards is paramount in industrial environments utilizing sodium hypochlorite. Organizations must adhere to strict guidelines regarding the proper labeling and placement of sodium hypochlorite placards. The regulatory framework not only mandates the presence of these placards but also governs their maintenance and visibility to guarantee maximum safety and risk mitigation.
Importance in Hazard Identification and Risk Mitigation
The sodium hypochlorite placard serves as a frontline defense mechanism in identifying potential hazards and minimizing risks in the workplace. By providing clear and concise information about the chemical present, these placards enable swift and informed decision-making during emergencies. Additionally, they facilitate appropriate response measures, ensuring the safety and well-being of all individuals in the vicinity.
Compliance Training and Awareness Programs
Establishing a robust framework for educating personnel on the significance of sodium hypochlorite placards is instrumental in fostering a culture of safety and adherence. Training programs should encompass placard recognition, emergency response protocols, and safety precautions related to sodium hypochlorite exposure. By prioritizing compliance training and awareness initiatives, organizations can enhance preparedness and proactive risk management strategies.
Conclusion
Introduction
In the realm of industrial safety, the sodium hypochlorite placard stands as a vital sentinel against potential hazards. This article delves into the meticulous significance behind this unassuming yet crucial signage within industrial environments. From its composition to its regulatory demands, the sodium hypochlorite placard plays a pivotal role in safeguarding both workers and the public from looming dangers. Understanding its nuances and pivotal significance is quintessential for fostering a culture of safety and adherence within industries relying on this chemical compound.
Overview of Sodium Hypochlorite
Chemical Properties
Delving into the chemical properties of sodium hypochlorite uncovers a realm of crucial factors that dictate its usage and handling protocols. With its bleach-like properties, sodium hypochlorite serves as a potent disinfectant, owing to its ability to combat pathogens effectively. Its oxidizing nature enables it to break down organic compounds, making it a popular choice in disinfection processes within various industries. However, its corrosive potential necessitates careful handling to avert unwanted chemical reactions and ensure employee safety.
Common Uses
Sodium hypochlorite finds extensive application across diverse industries, primarily as a disinfectant and bleaching agent. From water treatment plants to agricultural settings, its versatility makes it a go-to solution for sterilization and whitening purposes. Despite its array of benefits, caution must be exercised due to its potential reactivity with other chemicals, emphasizing the need for stringent safety measures during storage and application.
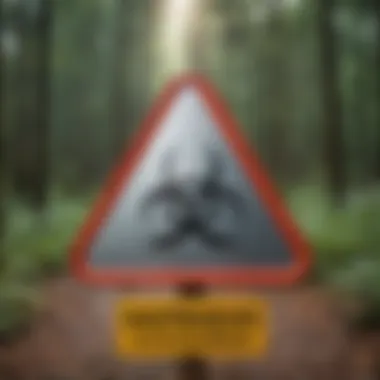

Potential Hazards
Exploring the potential hazards associated with sodium hypochlorite reveals a spectrum of risks that demand meticulous attention. Its corrosive nature poses a threat to both human health and the environment, underscoring the critical importance of proper handling and storage. Contact with skin or inhalation of fumes can lead to severe burns and respiratory complications, necessitating comprehensive safety protocols to mitigate these risks effectively.
Importance of Industrial Safety
Protecting Workers
The paramount importance of the sodium hypochlorite placard in protecting workers cannot be overstated. By alerting employees to the presence of this potentially hazardous substance, the placard serves as a frontline defense mechanism, fostering heightened awareness and caution. Ensuring workers understand the risks associated with sodium hypochlorite is essential for preventing accidents and safeguarding their well-being within industrial settings.
Preventing Accidents
Beyond directly safeguarding workers, the sodium hypochlorite placard plays a pivotal role in accident prevention within industrial facilities. By highlighting the dangers associated with sodium hypochlorite, the placard serves as a visual reminder of the need for careful handling and adherence to safety protocols. This proactive approach significantly reduces the likelihood of accidents and enhances overall workplace safety.
Legal Regulations
Compliance with legal regulations surrounding sodium hypochlorite usage is imperative for industrial operations. From OSHA standards to environmental regulations, strict guidelines govern the handling, storage, and disposal of this chemical compound. Failure to adhere to these regulations not only jeopardizes worker safety but also exposes organizations to potential legal ramifications, emphasizing the absolute necessity of compliance for a safe and sustainable work environment.
Understanding Sodium Hypochlorite Placard
Sodium hypochlorite placards are essential components in industrial environments where this chemical is present. These placards serve as crucial identifiers, alerting workers and the public to the presence of sodium hypochlorite and the potential hazards associated with it. Understanding these placards is paramount in promoting a culture of safety and compliance within industrial facilities. By familiarizing oneself with the composition, design, and regulatory requirements of sodium hypochlorite placards, individuals can contribute significantly to creating a secure working environment.
Composition and Design
Color Codes
Color coding plays a pivotal role in sodium hypochlorite placards, aiding in quick identification of the chemical and its associated risks. The use of distinct colors on the placard helps in immediately differentiating sodium hypochlorite from other substances, enhancing overall safety measures. The choice of colors for sodium hypochlorite placards is not arbitrary; it is based on industry standards and protocols to ensure universal recognition and understanding. Highlighting the color codes on these placards fulfills the crucial function of providing visual cues for potential dangers related to sodium hypochlorite, thus enabling quick and informed decision-making in emergency situations.
Symbolic Representations
Symbolic representations on sodium hypochlorite placards offer additional layers of information beyond color codes. These graphical symbols are universally recognized safety signs that convey specific instructions or warnings regarding sodium hypochlorite. Their presence on the placard enhances comprehension for individuals who may not be familiar with the language used in the accompanying text. The symbolic representations are designed to be intuitive and straightforward, serving as effective visual aids for communicating critical safety information associated with sodium hypochlorite. Incorporating these symbols into the placard design ensures clarity and consistency in conveying safety messages.
Information Displayed
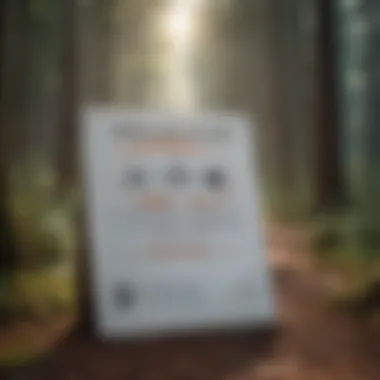
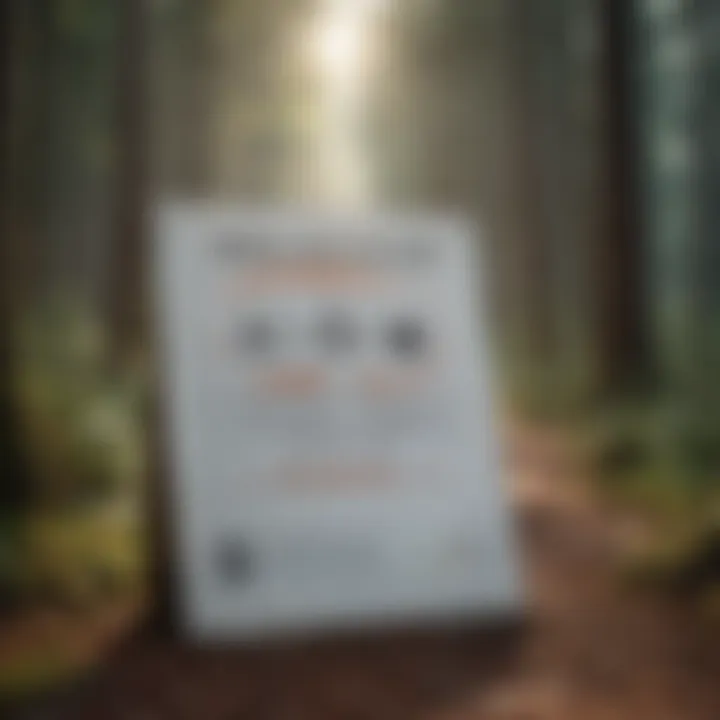
The information displayed on sodium hypochlorite placards follows standardized formats to convey essential details effectively. From chemical names and hazard levels to emergency contact information, these placards provide comprehensive data pertaining to sodium hypochlorite. By prominently featuring this information in a clear and structured manner, sodium hypochlorite placards facilitate quick reference during emergencies, enabling responders to act swiftly and decisively. The details displayed on these placards undergo regulatory scrutiny to ensure accuracy and relevance, reflecting a commitment to upholding safety standards and promoting awareness in industrial settings.
Placement and Accessibility
Visibility Requirements
Ensuring the visibility of sodium hypochlorite plature anticipation of potential hazards and facilitate timely response to emergencies.
Distance Regulations
Maintaining specific distances between sodium hypochlorite storage areas and other facilities is critical for safety. Distance regulations outlined for sodium hypochlorite placards aim to minimize risks associated with chemical exposure and accidental spills. These regulations dictate the spatial arrangement of sodium hypochlorite storage units in relation to designated work areas, emergency exits, and public spaces. Compliance with distance regulations enhances workplace safety by creating buffer zones that mitigate the impact of any untoward incidents involving sodium hypochlorite.
Language Specifications
The language used on sodium hypochlorite placards must prioritize clarity and comprehension. Language specifications denote the linguistic requirements for conveying safety information effectively to individuals across different linguistic backgrounds. Whether through multilingual text or internationally recognized symbols, language specifications aim to transcend language barriers and ensure universal understanding of sodium hypochlorite hazards. Adhering to prescribed language specifications on placards strengthens communication strategies, facilitating swift action and cohesive response protocols in diverse industrial settings.
Regulatory Compliance
OSHA Standards
Requirements for Industries
When addressing the OSHA standards pertinent to sodium hypochlorite placard usage, the requirements set forth for industries play a crucial role in establishing safe practices. These requirements outline the specific protocols and guidelines that industrial facilities must follow regarding the handling, storage, and labeling of sodium hypochlorite. By delineating clear procedures and safety measures, the requirements for industries serve as a foundation for ensuring a secure working environment. Their emphasis on proper containment, ventilation, and emergency response procedures significantly contribute to hazard prevention and risk mitigation.
Training Obligations
Within the framework of OSHA standards, the training obligations related to sodium hypochlorite placard implementation are fundamental in promoting awareness and preparedness among workers. Training programs encompassing the identification of placards, understanding chemical properties, and responding to emergencies are essential for equipping employees with the knowledge and skills needed to handle sodium hypochlorite safely. By fulfilling training obligations, industries enhance employee competencies, reduce the likelihood of accidents, and demonstrate a commitment to professional development and workplace safety.
Enforcement Measures
Enforcement measures associated with OSHA standards serve as a pivotal mechanism for upholding regulatory compliance and ensuring accountability within industrial settings. These measures encompass inspections, audits, and enforcement actions carried out by regulatory bodies to assess industry compliance with sodium hypochlorite safety regulations. Through stringent enforcement, regulatory bodies can identify non-compliance issues, levy sanctions, and institute corrective actions to rectify safety deficiencies. The enforcement of standards acts as a deterrent against negligent practices, fostering a culture of adherence to safety protocols and regulatory requirements for sodium hypochlorite handling.
Compatibility Issues
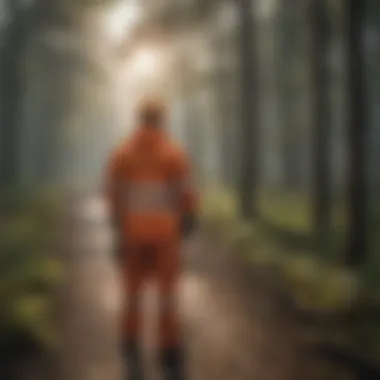
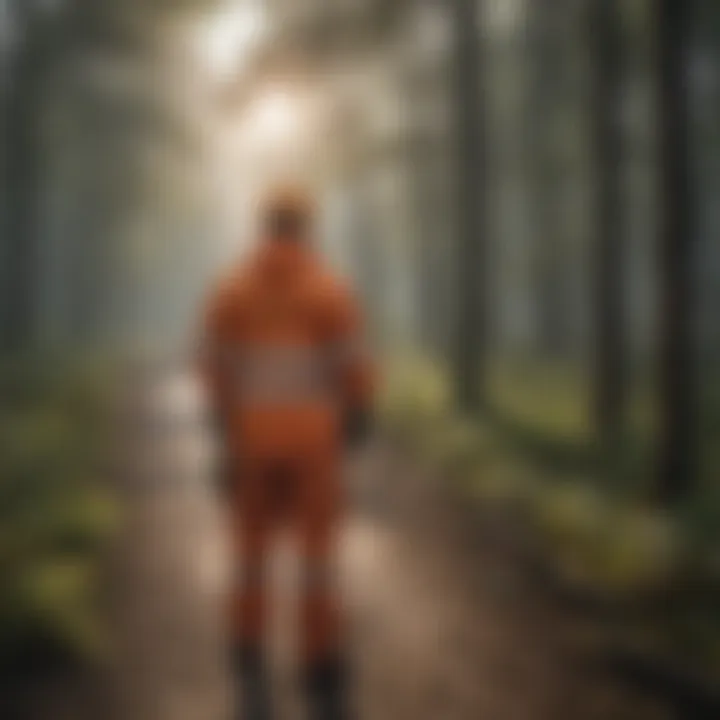
Addressing compatibility issues within the realm of sodium hypochlorite storage is a nuanced endeavor that requires a thorough understanding of chemical interactions and material suitability. Compatibility issues can arise when sodium hypochlorite comes into contact with certain substances or materials, leading to detrimental effects such as corrosion, chemical reactions, or compromised containment. It is imperative to select storage solutions that are chemically compatible with sodium hypochlorite to prevent accidents and ensure the integrity of the storage system. Highlighting potential incompatibilities and proactively addressing them through proper segregation and labeling of materials is paramount in minimizing risks. While navigating compatibility issues may pose challenges in storage management, industry-specific guidelines and expert consultation can offer valuable insights into mitigating risks effectively. By acknowledging and mitigating compatibility issues, industries can uphold stringent safety standards and foster a secure environment for handling sodium hypochlorite.
Emergency Response Procedures
Emergency response procedures are of utmost importance in ensuring workplace safety, particularly in environments where sodium hypochlorite is present. Prompt and efficient responses to emergencies such as spills are critical to mitigating risks and preventing accidents. By having well-defined emergency protocols in place, organizations can minimize the impact of incidents and protect both employees and the surrounding community. This section will delve into the key components of emergency response procedures, their role in industrial safety, and the necessary considerations for effective implementation.
Spill Management
Spills of sodium hypochlorite can pose significant dangers to both human health and the environment. Implementing robust spill management strategies is essential for containing and controlling spills effectively. By focusing on containment strategies, personal protective equipment, and decontamination protocols, organizations can streamline their response to spills and limit the potential consequences.
Containment Strategies
When a spill occurs, the first step is to swiftly contain the hazardous material to prevent it from spreading further. Containment strategies involve using barriers, absorbent materials, and specialized equipment to confine the spill to a localized area. The key characteristic of effective containment strategies is their ability to limit the extent of contamination and reduce the risk of exposure to workers and the environment. This targeted approach enhances safety measures and promotes a swift resolution to the spill incident.
Personal Protective Equipment
Equipping personnel with the appropriate personal protective equipment (PPE) is vital during spill response activities. PPE such as gloves, goggles, and respiratory protection safeguards workers from potential exposure to hazardous substances. The key characteristic of reliable PPE is its ability to provide a physical barrier between the individual and the hazardous material, minimizing the risk of contamination. By prioritizing the use of PPE, organizations demonstrate their commitment to employee safety and ensure proper precautions are taken during spill response operations.
Decontamination Protocols
Following a spill event, thorough decontamination protocols must be implemented to remove any traces of the hazardous substance from affected surfaces or equipment. Decontamination procedures involve cleaning, disinfecting, and verifying that the area is safe for re-entry. The unique feature of decontamination protocols lies in their ability to eliminate residual contamination and reduce the risk of secondary exposure. By adhering to established decontamination protocols, organizations can restore safety conditions and prevent potential health hazards for workers and responders.
Conclusion
Ensuring workplace safety is paramount in any industrial setting. It encompasses a range of practices and procedures aimed at safeguarding the well-being of workers and the public. In the context of this article, ‘Ensuring Workplace Safety’ holds a pivotal position. By emphasizing continuous training, periodic inspections, and community awareness, companies can create a culture of safety consciousness that permeates all levels of their operations. This holistic approach not only minimizes accidents and injuries but also fosters productivity and compliance with regulatory standards. Thus, the significance of this subject cannot be overstated within the industrial landscape.
Ensuring Workplace Safety
Continuous Training
Continuous training stands out as a cornerstone in promoting workplace safety. This ongoing process equips employees with the necessary knowledge and skills to handle hazardous materials like sodium hypochlorite effectively. By addressing the specific intricacies of working with such chemicals, continuous training enhances workers' competency levels, reducing the likelihood of accidents. Its structured nature ensures that employees are updated on the latest safety protocols and best practices, thus fostering a culture of vigilance and compliance. The advantage of continuous training lies in its proactive approach, preempting potential risks before they escalate. However, scheduling regular training sessions can be resource-intensive and time-consuming, posing a challenge for some organizations.
Periodic Inspections
Periodic inspections serve as a vital component of ensuring workplace safety, offering a systematic way to identify and rectify potential hazards. By conducting routine assessments of equipment, storage facilities, and adherence to safety protocols, companies can uphold high standards of safety. The key characteristic of periodic inspections lies in their preventive nature, enabling organizations to detect safety lapses before they lead to accidents. This proactive measure not only safeguards employees but also enhances operational efficiency by minimizing downtime due to unforeseen safety issues. However, the drawback of periodic inspections is the risk of oversight, especially in large industrial setups where thorough monitoring can be challenging.
Community Awareness
Community awareness plays a crucial role in promoting workplace safety beyond company boundaries. By engaging with local communities and stakeholders, organizations can enhance awareness about industrial safety practices and potential hazards associated with chemicals like sodium hypochlorite. The key characteristic of community awareness initiatives is their ability to create a sense of shared responsibility towards safety, fostering collaboration between businesses and the community. This outreach not only enhances public trust in industrial operations but also prepares communities to respond effectively in case of emergencies. However, sustaining community awareness requires consistent effort and resources, making it imperative for companies to integrate safety communication strategies into their long-term planning.