High Performance Plastics: Insights and Applications
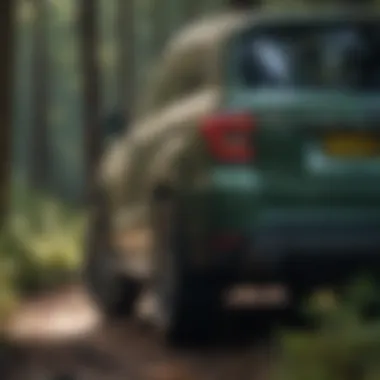
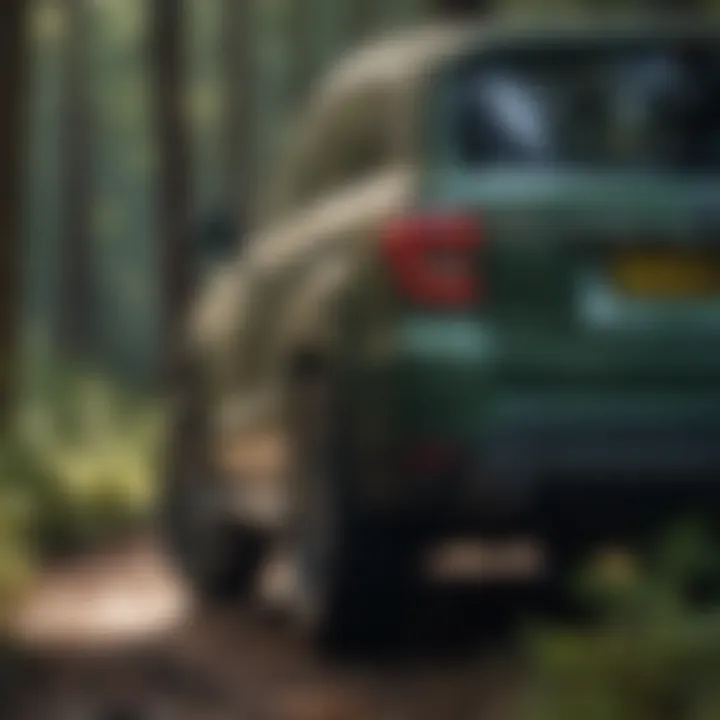
Intro
High performance plastics have emerged as crucial materials in various industrial sectors due to their unique properties. Unlike conventional plastics, these materials offer superior strength, high-temperature resistance, and enhanced chemical stability. Their applications are diverse, ranging from aerospace components to medical devices. Understanding the characteristics of high performance plastics is essential for professionals and researchers in material sciences, engineering, and sustainability fields.
The exploration of high performance plastics is timely, given the increasing demand for innovative materials that meet stringent performance criteria while also addressing environmental concerns. This article aims to elucidate the significant attributes of these plastics, their roles in different industries, and the challenges associated with their production and recycling.
Through this comprehensive discussion, readers will gain valuable insights into the future possibilities of high performance plastics, shaping a more sustainable approach in modern industrial landscape.
Key Properties of High Performance Plastics
High performance plastics exhibit distinct characteristics that set them apart from standard plastic materials. These properties include:
- Temperature Resistance: They can maintain their mechanical properties at elevated temperatures, making them suitable for applications in the automotive and aerospace industries.
- Chemical Resistance: Many high performance plastics resist corrosive substances, which is crucial in chemical processing environments.
- Dimensional Stability: These materials demonstrate low shrinkage and expansion, ensuring precise tolerances in engineering applications.
- Electrical Insulation: Some high performance plastics serve as excellent electrical insulators, vital in electronics and wiring.
These properties underscore the relevance of high performance plastics across various sectors, providing a robust alternative to metals and ceramics in demanding situations.
Applications in Modern Industries
High performance plastics find their way into many modern industries, reflecting their versatility and efficiency. Below are some key sectors utilizing these materials:
Aerospace Industry
In aerospace applications, high performance plastics are invaluable. They reduce weight while maintaining strength, contributing to fuel efficiency and performance of aircraft. For instance, polyetheretherketone (PEEK) is commonly used in components like bearings and seals.
Automotive Sector
The automotive industry leverages high performance plastics for parts such as fuel tanks and under-the-hood components. They enhance safety, performance, and longevity. Polysulfone (PSU) and polyamide (PA) are examples that provide excellent resistance to various automotive fluids and temperatures.
Medical Devices
Medical technology is another significant application area. High performance plastics are employed in surgical instruments and implants due to their biocompatibility and sterilization capabilities. Materials like polycarbonate (PC) and PEEK are well-suited for these uses.
Electronics
In the electronics realm, these materials serve to insulate components and enhance durability. Their chemical resistance and thermal stability make them ideal for circuit boards and connectors, ensuring reliable operation in varying conditions.
Challenges in Production and Recycling
Despite their advantages, high performance plastics present challenges in both production and recycling. The manufacturing processes for these materials can be complex and costly, limiting their widespread adoption. Additionally, recycling them poses difficulties due to their unique chemical bonds, which are not easily broken down.
Efforts are ongoing to develop more sustainable production methodologies, aiming to minimize their environmental footprint. Understanding these challenges is critical for professionals in the industry as they strive for innovation without compromising ecological responsibilities.
Finale
In summary, high performance plastics are revolutionizing various industries with their superior properties and applications. Recognizing their potential contributes to advancements in technology and industry practices. With ongoing research and innovation, high performance plastics will likely play an even larger role in shaping sustainable futures in manufacturing and engineering.
Intro to High Performance Plastics
High performance plastics are increasingly becoming essential in various industries due to their unique characteristics. This section introduces their significance in sectors such as aerospace, automotive, medical, and electronics. Understanding these materials is crucial for professionals and researchers who are exploring innovative solutions.
Why High Performance Plastics Matter
These plastics stand out due to their ability to withstand high temperatures, chemical exposure, and mechanical stress. This resilience allows design engineers to create products that are not only durable but also lightweight. For example, materials like polyetheretherketone (PEEK) and polyimide are used in applications where conventional materials fail.
Applications and Benefits
The variety of applications for high performance plastics indicates their importance. Their lightweight nature enhances fuel efficiency in aerospace and automotive sectors. In the medical field, these materials ensure safety, longevity, and compliance with strict health regulations.
- Aerospace: Reducing weight while enhancing performance.
- Automotive: Improving fuel efficiency and reducing emissions.
- Medical devices: Meeting rigorous sanitation standards.
(Source: )
Considerations for Implementation
However, despite their advantages, challenges remain in integrating high performance plastics into existing production systems. Issues such as cost and material sourcing are pivotal for organizations looking to adopt these technologies. Thus, a thorough analysis is necessary to weigh the benefits against the drawbacks.
In summary, high performance plastics represent a transformative approach to material science. They are not merely a trend; they are integral to modern engineering solutions. As industries evolve, the continuous exploration and development of these materials will play a vital role in shaping future innovations.
Defining High Performance Plastics
High performance plastics represent a class of materials that are engineered to perform under challenging conditions. They exhibit superior mechanical, thermal, and chemical properties compared to standard plastics. This significance extends beyond basic functionality; it influences design, manufacturing, and sustainability approaches across various sectors.
High performance plastics are crucial in applications where traditional materials might fail. They can withstand extreme temperatures, resist aggressive chemicals, and maintain stability under heavy loads. Understanding high performance plastics involves recognizing specific traits that define them:
- Thermal Stability: Able to endure temperatures well beyond the limits of conventional plastics, making them ideal for aerospace and automotive engineering.
- Chemical Resistance: Show exceptional resilience to corrosive environments, essential for uses in chemical processing and medical devices.
- Mechanical Strength: Designed to withstand physical stress, high performance plastics ensure longevity and durability.
Each of these factors contributes to their classification as high performance materials. By defining these plastics clearly, professionals can better assess their applications and select appropriate materials for specific challenges. This understanding not only aids in innovation but also informs decisions related to material sourcing and environmental impacts.
High performance plastics often come with a higher initial cost. However, their benefits in terms of longevity and reduced failure rates can lead to cost savings over time. When evaluating these materials, it is important to balance these costs with their performance advantages.
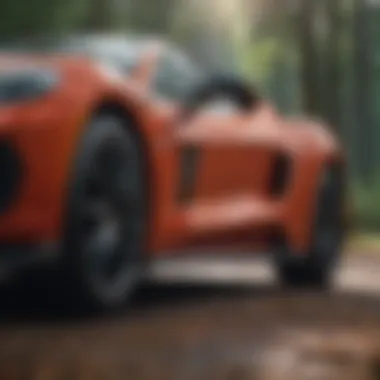
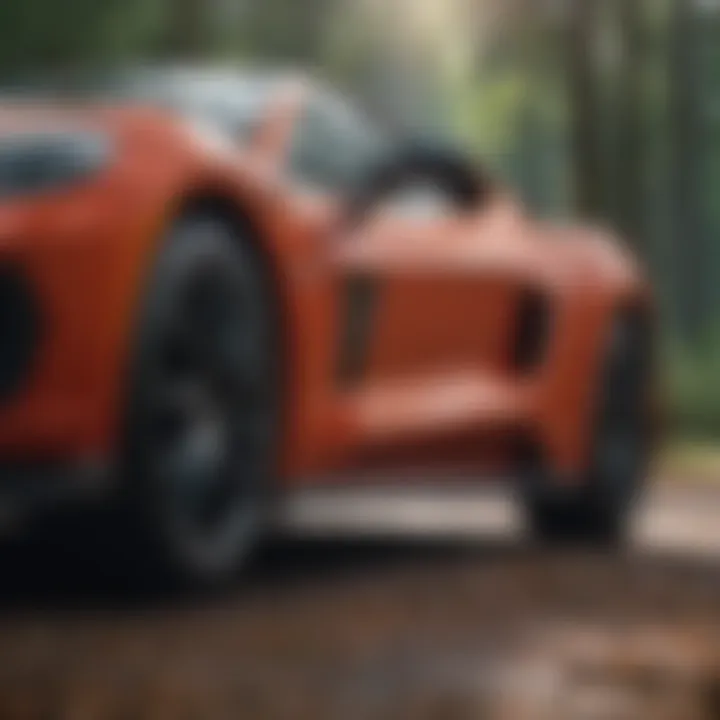
In summary, defining high performance plastics involves recognizing their unique attributes, applications, and the critical role they play in advanced industrial processes. Their properties make them indispensable for contemporary technology and sustainability efforts.
Material Composition and Properties
The composition and properties of high performance plastics are fundamental to their application and effectiveness across diverse industries. Understanding these materials requires delving into their unique characteristics and how they influence performance, safety, and sustainability.
Polymeric Structure
The polymeric structure defines the molecular arrangement of high performance plastics. These polymers are typically engineered to have a specific molecular weight and composition. Many high performance plastics are thermoplastics, which allow for reshaping upon heating, or thermosets that cure into a defined shape. This structural flexibility contributes to their wide usage in different environments. Factors such as molecular chain length and degree of crystallinity significantly affect properties like clarity, elasticity, and resistance to various stresses. For example, polyetheretherketone (PEEK) is renowned for its high-temperature resistance due to its strong covalent bonds.
Thermal and Chemical Resistance
Thermal and chemical resistance are distinguishing attributes of high performance plastics. They withstand extreme temperatures, making them suitable for high-heat applications in industries like aerospace and automotive. For instance, polyimide and fluoropolymers exhibit exceptional thermal stability.
Chemical resistance is equally crucial; these materials resist degradation from solvents and aggressive chemicals. This enables their use in environments where conventional materials might fail. The ability to endure chemical exposure is paramount for safety and resilience in medical devices and electronic components, where contamination or breakdown of materials can lead to catastrophic failures.
"High performance plastics are indispensable because they maintain integrity under adverse conditions."
Mechanical Strength and Durability
Mechanical strength and durability play a vital role in determining the lifespan and reliability of high performance plastics in applications. These materials exhibit impressive tensile strength, impact resistance, and fatigue performance. For example, aramid fibers used in composites for automotive components can withstand significant stress without failure.
The durability of these materials directly relates to performance over time. In industries like aerospace, where every gram matters, materials like polyamide-imide provide lightweight solutions that do not compromise on strength. Additionally, the ability to withstand wear and tear makes these plastics suitable for long-term applications, reducing the need for frequent replacements, leading to cost efficiencies.
By understanding the intricacies of material composition and properties, industries can leverage high performance plastics to meet their demanding requirements.
Applications Across Industries
High performance plastics have become indispensable across various sectors due to their unique characteristics such as strength, chemical resistance, and lightweight properties. The importance of these materials cannot be overstated when evaluating modern manufacturing and design strategies. In this section, we will explore multiple industries where high performance plastics are not just beneficial but often vital.
Aerospace Sector
In aerospace, the use of high performance plastics significantly contributes to weight reduction. Lightweight materials enhance fuel efficiency which is crucial in today’s environmentally conscious world. Components made from polyether ether ketone (PEEK) and polyimide are often used in aircraft interiors and structural elements. These plastics can withstand extreme temperatures and resist harsh chemicals.
Major considerations in this sector include:
- Material Certificaiton: Compliance with strict aviation regulations is necessary.
- Performance Standards: High performance plastics must endure rigorous testing for mechanical integrity.
- Weight vs. Strength Trade-offs: Finding the balance between reduced weight and needed durability is critical.
Automotive Engineering
The automotive industry significantly benefits from high performance plastics in several applications. These materials help in reducing overall vehicle weight without sacrificing safety. For instance, the use of polyamide in engine components leads to enhancements in fuel efficiency and emissions reduction. Moreover, they provide excellent thermal and electrical insulation.
Key aspects to note include:
- Safety Features: Many modern vehicles utilize high performance plastics in safety-critical components.
- Design Flexibility: Advanced manufacturing techniques allow detailed designs that were not possible before.
- Sustainability: Using these plastics can lead to greener manufacturing processes and products.
Medical Devices
The medical industry utilizes high performance plastics for their biocompatibility and sterilization capabilities. Materials like polyphenylsulfone (PPSU) and polyethylene terephthalate (PET) are commonplace in surgical tools, prosthetics, and medical packaging. Their ability to tolerate high temperatures is vital for sterilization, ensuring patient safety.
Consider these factors in medical applications:
- Regulatory Compliance: Devices must adhere to stringent regulatory frameworks.
- Durability and Longevity: The lifespan of medical devices can directly impact patient care outcomes.
- Cost Efficiency: While high performance plastics sometimes appear costly, their long-term benefits can offset initial investment.
Electronics and Consumer Goods
In electronics, high performance plastics provide insulation and protection for various components from moisture and temperature changes. Materials such as acrylonitrile butadiene styrene (ABS) and polycarbonate are found in casings and internal parts of gadgets. Their lightweight nature reduces the overall bulk of devices, making them more user-friendly.
The important highlights for this sector include:
- Impact Resistance: High performance plastics provide excellent protection against drops and impacts.
- Thermal Management: Certain formulations manage heat effectively, ensuring reliable operation.
- Aesthetics and Design: The versatility in design allows for appealing product designs that enhance user experience.
High performance plastics exemplify the intersection of innovation and practicality, providing tailored solutions in various industries.
Innovative Manufacturing Techniques
Innovative manufacturing techniques play a crucial role in the development, production, and application of high performance plastics. These methods not only enhance the capabilities of these materials but also contribute to efficiency, sustainability, and cost-effectiveness in various industries. Understanding these techniques is key to experts aiming for optimal utilization in their fields.
Additive Manufacturing
Additive manufacturing, often referred to as 3D printing, has revolutionized the way high performance plastics are produced. This method allows for layer-by-layer construction of parts, which means complex geometries can be created with relative ease. Traditional manufacturing often involves subtracting material, leading to waste. In contrast, additive manufacturing minimizes waste and allows for the efficient use of materials.
The benefits are numerous:
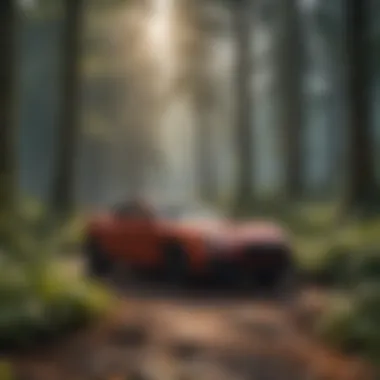
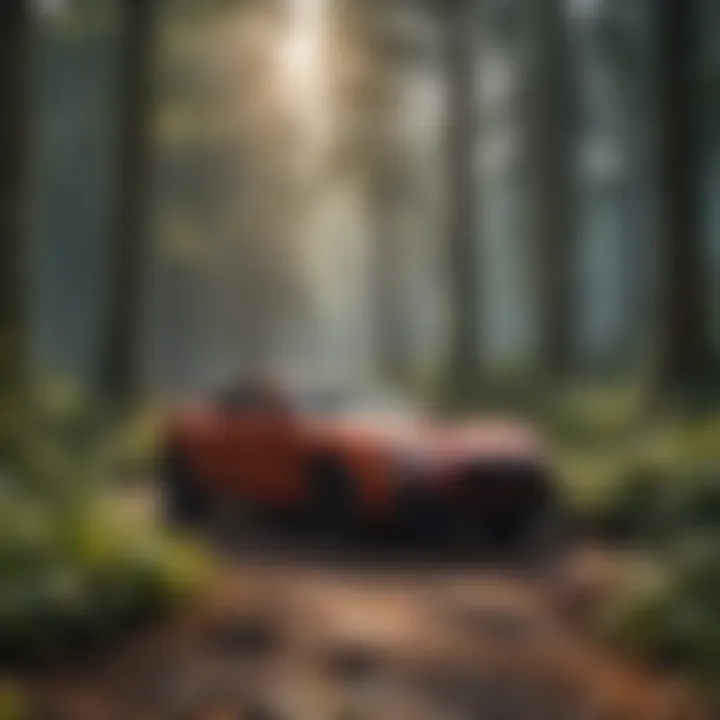
- Design Flexibility: Engineers can produce shapes and structures not possible with conventional processes.
- Rapid Prototyping: Products can be designed and modified quickly, reducing time to market.
- Customization: Each part can be tailored to specific needs without significant additional costs.
- Material Efficiency: Less waste as only the necessary amount of material is used for production.
Injection Molding Processes
Injection molding processes are another significant method in working with high performance plastics. This technique involves injecting molten plastic into a mold, allowing for high precision and repeatability. Injection molding is particularly useful when large volumes of parts are needed swiftly and with consistent quality.
Advantages include:
- Speed: This process is efficient for mass production, reducing cycle times.
- Quality Control: High consistency in product output ensures reliability in performance.
- Versatility: A wide range of high performance plastics can be molded to meet specific industry requirements.
Industry professionals often rely on injection molding for components in sectors like automotive and electronics, owing to the robustness and dimensional accuracy it provides.
Extrusion Techniques
Extrusion techniques are fundamental in shaping high performance plastics into continuous profiles, such as sheets, films, and rods. This process involves forcing the polymer through a die to create long shapes. The ability to produce large quantities of material in a continuous manner has made extrusion a favored method.
The key benefits of extrusion techniques are:
- Efficiency: High throughput rates can significantly reduce production time.
- Customization: Different profiles can be produced to fulfill diverse application needs.
- Cost-Effectiveness: Overall production costs can be lower due to economies of scale.
Recognizing the significance of these innovative manufacturing techniques is essential for professionals in the field. They not only define how high performance plastics are produced but also influence their performance and applications across various industries.
"Innovative manufacturing techniques enhance not just the products but the entire process, providing a competitive edge in modern industries."
In summary, understanding these manufacturing methods enables industries to leverage the full potential of high performance plastics, driving progress in their respective sectors.
Challenges in Development and Implementation
The development and implementation of high performance plastics present various challenges that must be navigated to maximize their potential in modern applications. Understanding these challenges is crucial for industries relying on these materials. The complexities involved stem from economic, technical, and environmental dimensions. By addressing these challenges effectively, we can enhance the performance and sustainability of high performance plastics in strategic sectors.
Cost vs. Performance Trade-offs
Performance is a fundamental criterion in selecting plastics for specific applications. However, achieving optimal performance often comes at a higher cost. High performance plastics like polyether ether ketone (PEEK) and polyimide offer exceptional mechanical and thermal properties. Yet, their production costs can be significantly higher than conventional plastics. This creates a notable trade-off for manufacturers and engineers. Industries must weigh the benefits of enhanced performance against the financial implications.
Some questions may arise:
- Will the increased longevity and reduced maintenance costs offset initial investments?
- How does the performance of high performance plastics compare to less expensive alternatives in critical applications?
Making informed decisions requires comprehensive analysis of both short-term and long-term costs, often leading to intricate evaluations of project budgets and operational expenses.
Material Sourcing and Availability
Material sourcing remains a pivotal challenge in the high performance plastic landscape. Obtaining reliable sources of high-grade raw materials is vital for consistent production quality. Many high performance plastics require specialized polymers or additives that are not as readily available as standard materials.
Factors influencing material sourcing include:
- Global Supply Chains: Political and economic uncertainties can disrupt supply chains, making it hard to source materials reliably.
- Supplier Dependability: Finding suppliers who meet strict quality standards is essential.
- Market Demand: If demand for high performance plastics grows, sourcing can become even more problematic.
These factors underline that companies must develop robust strategies for material procurement to ensure smooth production workflows.
Recycling Issues and Environmental Impact
The environmental impact of high performance plastics has become a central concern. While these materials offer durability and long life, their resistance to degradation poses challenges for recycling and waste management. Many high performance plastics do not fit into traditional recycling streams, complicating sustainability efforts.
Considerations include:
- Recycling Processes: Advanced recycling technologies are often necessary to process these materials, but they are not yet widely adopted.
- Landfill Concerns: High performance plastics can contribute to landfill issues if not managed properly.
- Life Cycle Analysis: It's crucial to analyze the environmental impact from production to disposal, ensuring that performance benefits do not come at the expense of ecological sustainability.
"Sustainable practices in high performance plastics development must evolve alongside innovations in recycling technology."
Sustainability Considerations
Sustainability plays a crucial role in the discourse surrounding high performance plastics. As industries grow more aware of their environmental footprint, the need for sustainable practices becomes more pressing. High performance plastics have unique properties that lend themselves to various applications, yet their production and disposal present challenges. This section highlights the importance of considering sustainability in the context of material selection and lifecycle management.
Biodegradable Alternatives
One area of growth in sustainability is the development of biodegradable alternatives to conventional high performance plastics. These materials are designed to break down more readily in the environment, which helps to mitigate pollution. Companies are investing in research to identify materials that maintain performance while being more eco-friendly.
Examples of biodegradable plastics include polylactic acid (PLA) and polyhydroxyalkanoates (PHA). These materials can serve similar functions to traditional plastics in many applications, but they decompose into non-toxic byproducts. While not all applications are suitable for these alternatives, ongoing innovation aims to expand their utility in areas like packaging and consumer goods. The move towards biodegradable solutions represents an important step in reducing plastic waste.
Lifecycle Analysis of High Performance Plastics
Conducting a lifecycle analysis (LCA) of high performance plastics is essential for understanding their environmental impact from production to disposal. An LCA evaluates all stages of a product’s life, including raw material extraction, manufacturing processes, usage, and end-of-life treatment. This comprehensive approach sheds light on the sustainability credentials of a material, allowing for informed decision-making.
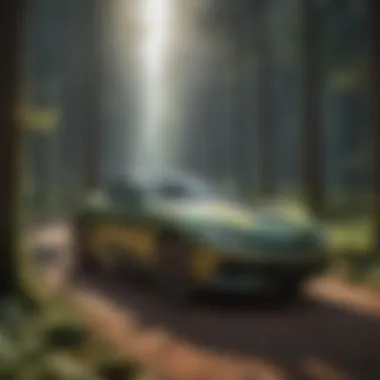
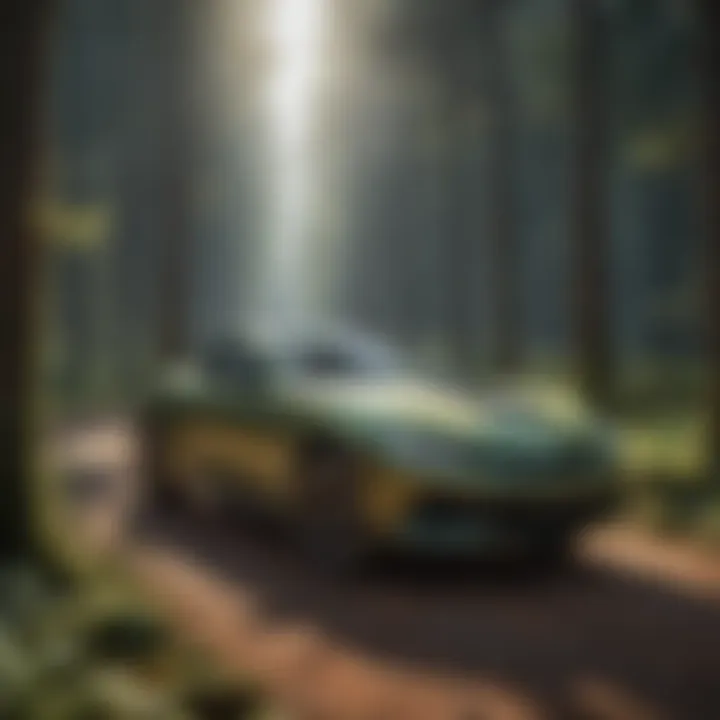
Key elements to consider in lifecycle analysis include:
- Energy Consumption: Assessing how much energy is used during the production processes and how this can be minimized.
- Carbon Footprint: Understanding the emissions associated with each phase and identifying opportunities for reduction.
- Recyclability: Evaluating how easily a material can be recycled or repurposed, which impacts its overall sustainability.
- Waste Management: Considering the end-of-life treatment options and their implications on the environment.
A well-conducted lifecycle analysis can reveal hidden inefficiencies and drive improvements in sustainable practices for high performance plastics.
The insights gained from LCA can spark innovation, guiding businesses toward more sustainable practices in both product development and material sourcing. Thus, integrating sustainability into the selection and application of high performance plastics is not just beneficial; it is imperative for future viability.
Future Trends in High Performance Plastics
In the evolving landscape of material science, the future of high performance plastics holds significant promise. These materials have far-reaching implications for various industries due to their adaptability and superior properties. Understanding these trends is essential for professionals aiming to innovate and implement these materials in practical applications.
Emerging Materials
The exploration of new raw materials is an ongoing journey in high performance plastics. Scientists are focusing on bio-based polymers that derive from renewable resources. Examples like polylactic acid (PLA) showcase how sustainable options can perform adequately in demanding environments. Emerging materials also include various composites and advanced ceramic resins that boast improved strength-to-weight ratios. This is vital in sectors like aerospace, where minimizing weight can lead to increased efficiency and reduced fuel consumption.
- Key Points of Emerging Materials:
- Bio-based options reduce reliance on fossil fuels.
- Composites allow for customized material properties, which meet specific applications.
- Each new material pushes the limits of traditional plastics, enhancing functionality.
Scientific research continues to shed light on these promising substances, often leading to unexpected innovations across different sectors.
Technological Advancements
Technological progress encapsulates critical changes in the production and application of high performance plastics. Advanced manufacturing techniques, such as 3D printing, are revolutionizing how products are designed and produced. This method allows for intricate designs that were previously impossible or too costly to manufacture using conventional methods.
Additionally, automation is streamlining processes, reducing waste, and increasing efficiency at production facilities. New tools in computational modeling help predict performance characteristics, guiding the development of tailored plastics for specific tasks.
"The integration of technology in material sciences not only enhances product quality but also fosters innovative solutions across industries."
- Advantages of Technological Advancements:
- Increases production efficiency and lowers costs.
- Enables rapid prototyping, reducing time to market.
- Enhances customization of materials to meet unique demands.
As technology progresses, we can expect a larger shift towards smart materials that can adapt to changing conditions, further enhancing their utility in modern applications.
Case Studies and Real-World Applications
Case studies offer concrete examples that illustrate the practical uses of high performance plastics. They shed light on the effectiveness, usability, and innovation in real-world scenarios. Understanding these applications deepen our grasp of how these materials shape modern industries. Through specific instances, professionals can evaluate the benefits, challenges, and potential of high performance plastics. This section discusses notable implementations in two critical sectors: aerospace and automotive engineering.
Successful Implementations in Aerospace
The aerospace industry is renowned for its stringent requirements in materials. High performance plastics play an essential role in this sector, providing lightweight yet durable solutions. For instance, Polyetheretherketone (PEEK) is used in aircraft interiors and components that must withstand high temperatures and pressures.
A prime example of PEEK’s implementation is in the Boeing 787 Dreamliner. The aircraft utilizes PEEK for various internal parts, allowing for reduced weight, improved fuel efficiency, and enhanced performance. Additionally, its chemical resistance is crucial in these environments, as materials often encounter challenging conditions.
Some benefits include:
- Weight reduction which directly enhances fuel efficiency
- Thermal stability enabling components to endure extreme conditions
- Cost efficiency in reducing maintenance and replacements over time
These elements demonstrate the impact of high performance plastics in enhancing innovation in aerospace design and functionality.
Innovations in Automotive Usage
The automotive sector has also experienced significant advancements thanks to high performance plastics. These materials contribute to both safety and efficiency. Polyamide (PA), for example, is often utilized in automotive components due to its strength and lightweight characteristics.
A notable case is the application of polyamide in engine covers and components of modern vehicles. Manufacturers such as Ford and BMW have incorporated this material to produce parts that not only meet rigorous performance standards but also comply with stringent emissions regulations.
Key advantages include:
- Enhanced mileage from weight reduction
- Flexibility in design allowing for innovative shapes and structures
- Improved safety through superior impact resistance
In both aerospace and automotive industries, high performance plastics have proven to be indispensable. The evidence from these case studies indicates not just immediate impact but also a clear trajectory for future innovations.
"High performance plastics are not merely materials but transformative solutions shaping the industries of tomorrow."
Continued research and adaptation are necessary to leverage their full potential. As industries evolve, so too must our approaches to utilizing these advanced materials.
End
The exploration of high performance plastics converges on several pivotal themes that underscore their significance in modern industry. This article has delved into the unique properties of these materials, highlighting their versatility and relevance across various sectors.
One key aspect is the exceptional physical and chemical attributes of high performance plastics. These materials often demonstrate superior thermal stability and resistance to aggressive chemicals, making them ideal for demanding applications in aerospace, automotive, and medical fields. Their mechanical strength further contributes to longevity, reducing the frequency of replacements and repairs.
The applications discussed reflect not only current trends but also the transforming landscape of material sciences. Industries have started to recognize the potential of high performance plastics to enhance product performance while also reducing overall weight, which is particularly advantageous in aerospace and automotive sectors. This shift aligns with global movements towards greater efficiency and sustainability.
Moreover, sustainability, a recurring theme in every section, cannot be overlooked. The potential integration of biodegradable alternatives and lifecycle analysis paves way for innovations that meet environmental standards. This is imperative in our quest to address the pressures of plastic waste and environmental degradation.
"High performance plastics hold the keys to the future of manufacturing, offering solutions that are both effective and sustainable."
Through this discourse, it is evident that the relevance and impact of high performance plastics will only grow. Adaptation and thoughtful incorporation of these materials into new applications signify strides towards innovation and responsibility in industry.