Unveiling the Wonders of Sheet Molding Composite: A Comprehensive Exploration
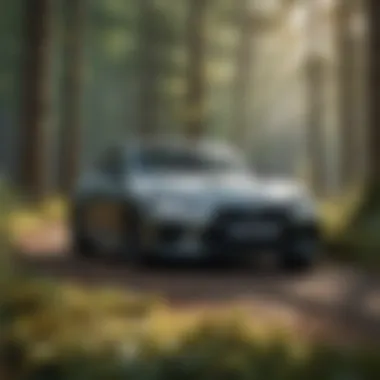
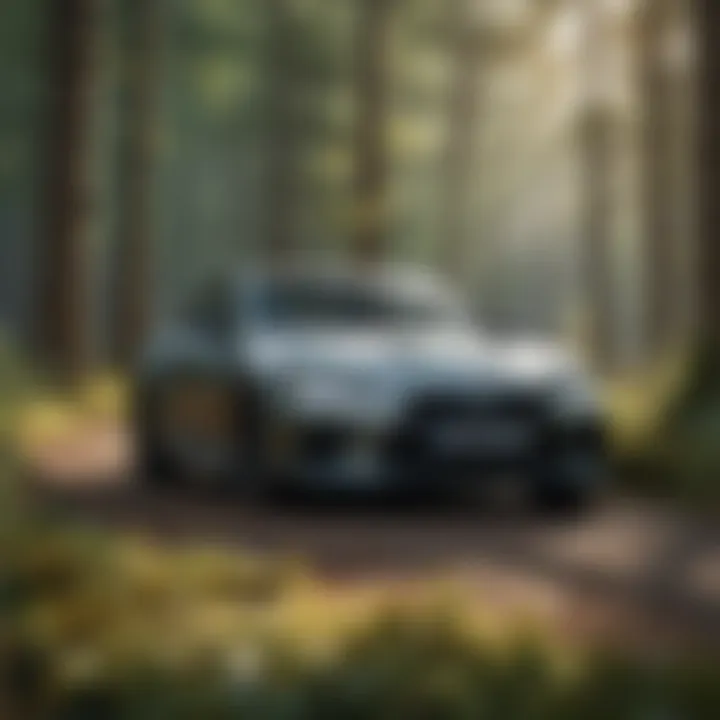
Evergreen Trees Species
Evergreen trees are a significant feature of American forests, offering a diverse array of species that contribute to the rich ecological tapestry of the landscape. From the iconic Douglas fir to the majestic redwood trees, exploring the types of evergreen trees found in these forests unveils a world of botanical wonder and natural beauty. These trees play a crucial role in providing habitat for a wide range of wildlife and promoting biodiversity within their ecosystems.
Ecological significance of evergreen trees goes beyond their visual appeal, as they play a vital role in maintaining the health of the forest ecosystem. Evergreen trees act as carbon sinks, sequestering carbon dioxide from the atmosphere and helping mitigate the impacts of climate change. Their year-round foliage provides shelter and food for various animal species, thereby promoting a healthy and balanced ecosystem.
To preserve evergreen tree species, it is imperative to implement conservation practices that aim to protect these valuable resources. Conservation methods such as sustainable logging practices, habitat preservation, and reforestation efforts are crucial in ensuring the longevity and vitality of evergreen forests. By highlighting the importance of these practices, we can work towards safeguarding these iconic trees for future generations to appreciate and enjoy.
Introduction to Sheet Molding Composite
In this comprehensive exploration of Sheet Molding Composite (SMC), we delve into the intricate world of a material that has revolutionized various industries. The significance of understanding the intricacies of SMC lies in its widespread applications and unique properties that set it apart from traditional materials. By familiarizing ourselves with the composition, manufacturing processes, and key characteristics of SMC, we are better equipped to appreciate its vital role in modern engineering and design.
Definition and Composition
Resin
The resin component of SMC plays a crucial role in determining the material's final properties. Resin acts as the bonding agent that holds together the reinforcements and fillers, contributing to the overall strength and durability of the composite. One of the key characteristics of resin is its ability to provide excellent adhesion to various materials, enhancing the structural integrity of the final product. This adhesive property makes resin a popular choice in SMC production, ensuring a strong and reliable composite. Despite its advantages, resin may pose challenges such as curing time variability, requiring precise control during the manufacturing process.
Reinforcements
Reinforcements are essential elements in SMC that enhance the mechanical properties of the composite. By adding strength and stiffness, reinforcements improve the structural integrity of the material, making it suitable for a wide range of applications. The unique feature of reinforcements lies in their ability to distribute stress evenly across the composite, reducing the likelihood of failure under load. While reinforcements offer significant advantages in terms of strength and performance, they may also increase the overall weight of the final product, influencing design considerations.
Fillers
Fillers in SMC serve multiple purposes, including reducing resin usage, controlling shrinkage, and enhancing specific properties such as thermal conductivity. By adjusting the filler composition, manufacturers can tailor the final product to meet specific requirements, providing versatility in material selection. The key characteristic of fillers is their ability to lower production costs while maintaining desirable physical characteristics, making them a cost-effective choice in SMC production. However, fillers may impact certain properties, such as stiffness, depending on the type and amount incorporated into the composite.
Advantages of SMC
High Strength
The exceptional strength of SMC makes it a preferred choice in applications where structural integrity is paramount. With a high tensile and flexural strength, SMC offers outstanding performance under varying loads, ensuring durability in demanding conditions. The unique feature of high strength in SMC enables the material to withstand heavy impacts and stresses, making it ideal for applications requiring resilience and longevity. While high strength enhances the reliability of SMC, it may also increase production costs due to the need for precise manufacturing processes.
Lightweight
SMC's lightweight nature sets it apart from conventional materials like steel or aluminum, offering a balance between strength and weight savings. The key characteristic of lightweight SMC lies in its ability to reduce overall vehicle weight, leading to improved fuel efficiency and lower emissions in the automotive industry. The unique feature of lightweight SMC extends to other applications where weight reduction is a crucial factor in enhancing performance and efficiency. Despite its benefits, the lightweight property of SMC may necessitate additional design considerations to ensure structural integrity and support specific load requirements.
Corrosion Resistance
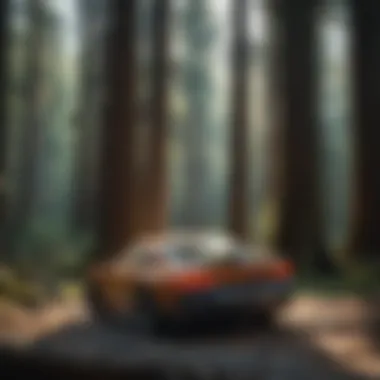
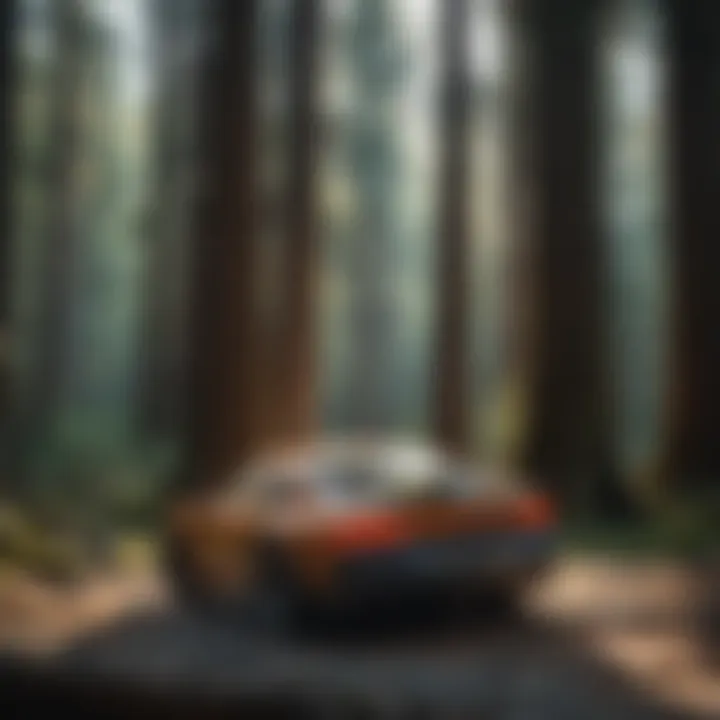
Corrosion resistance is a key advantage of SMC, particularly in industries where exposure to harsh environmental conditions is common. By inherently resisting corrosion, SMC provides superior longevity and durability compared to traditional materials prone to degradation. The unique feature of corrosion resistance in SMC ensures minimal maintenance and extended service life, reducing overall lifecycle costs. While corrosion resistance offers significant benefits in terms of sustainability and performance, it may present challenges during the manufacturing process, requiring specialized techniques to achieve optimal properties.
Applications of SMC
Automotive Industry
The automotive industry extensively relies on SMC for its exceptional properties, including high strength-to-weight ratio, corrosion resistance, and design flexibility. SMC components in vehicles contribute to weight reduction, fuel efficiency improvement, and enhanced safety standards, making it a preferred material for manufacturers aiming to meet stringent regulations and consumer demands. The unique feature of SMC in the automotive sector lies in its ability to address diverse requirements, from exterior body panels to structural components, showcasing its versatility and reliability in a competitive market.
Electrical Enclosures
SMC's electrical insulating properties and flame-retardant characteristics make it an ideal choice for electrical enclosures requiring protection against environmental factors and electrical hazards. Widely used in electrical infrastructure, SMC enclosures offer superior performance in harsh conditions, ensuring equipment reliability and safety. The key characteristic of electrical enclosures made from SMC is their ability to provide insulation and protection, safeguarding sensitive components from external influences. Despite its advantages, the insulating properties of SMC may impact heat dissipation, necessitating careful design considerations for efficient operation.
Building Materials
In the construction sector, SMC finds applications in various building materials such as cladding panels, roofing systems, and structural components due to its lightweight, durable, and weather-resistant properties. SMC's ease of molding into complex shapes and customizable finishes makes it an attractive choice for architects and designers seeking innovative solutions for modern construction challenges. The unique feature of SMC in building materials lies in its ability to combine aesthetics with functionality, offering sustainable and cost-effective alternatives to traditional construction materials. However, the limitations of SMC in terms of thermal conductivity and fire resistance may require additional measures to ensure compliance with building codes and safety standards.
Manufacturing Process of SMC
In this section, we will delve into the intricate process behind manufacturing Sheet Molding Composite (SMC), shedding light on the crucial steps involved in creating this versatile material. The manufacturing process of SMC holds immense importance in our exploration of this topic, as it plays a significant role in shaping the properties and applications of the final product. By understanding the specific elements, benefits, and considerations related to the manufacturing process of SMC, we can gain a deeper appreciation for the technical precision required in producing SMC components for various industries.
Compression Molding
Preforming
Preforming is a fundamental stage within the compression molding process of SMC, involving the shaping and preparation of the raw materials before the actual molding takes place. This preparatory step sets the foundation for the desired geometry and physical characteristics of the end product. Preforming is a critical aspect as it determines the uniformity and strength of the final composite, making it a foundational element in achieving high-quality SMC components. The key characteristic of preforming lies in its ability to control the fiber orientation and distribution, ensuring optimal mechanical properties in the finished part. Despite its necessity in the manufacturing process, preforming can be time-consuming and may require specialized equipment, presenting both advantages in product quality and potential drawbacks in production efficiency.
Molding
Molding is the central phase where the preformed SMC materials are placed into a mold cavity and shaped under heat and pressure to achieve the desired form. This step is instrumental in consolidating the resin and reinforcement materials to create a cohesive structure with specified dimensions. The key characteristic of molding is its ability to transform the raw SMC into a solid, durable composite part through controlled application of temperature and pressure. Molding's versatility and scalability make it a popular choice in the manufacturing of complex SMC products, offering greater design freedom and consistent quality. However, variations in molding parameters can impact the overall integrity of the composite, emphasizing the need for precise control and monitoring during the process.
Curing
Curing is the final stage in the compression molding process where the molded SMC part undergoes a curing cycle to solidify and strengthen the resin matrix. During curing, heat is applied to initiate resin cross-linking, enhancing the mechanical properties and dimensional stability of the composite. The key characteristic of curing lies in its role in developing the structural integrity and performance characteristics of the SMC component, ensuring long-term durability and reliability in service. While curing contributes significantly to the material's final properties, improper curing conditions or inadequate post-curing treatment can lead to defects like voids or insufficient mechanical strength, highlighting the importance of meticulous control and optimization in the curing process.
Sheet Molding Compound (SMC) Preparation
Mixing
Mixing stands as a critical aspect in the preparation of SMC, involving the homogenous blending of resin, reinforcements, and additives to form the composite paste. The key characteristic of mixing is its ability to ensure a uniform distribution of constituents to enhance the overall integrity and performance of the final SMC material. Proper mixing plays a vital role in optimizing the consistency and flow behavior of the compound, facilitating smooth molding and consolidation in subsequent processing stages. Though mixing contributes significantly to product quality and consistency, inadequate mixing can result in material inconsistencies and defects, underscoring the need for controlled mixing parameters and thorough quality checks.
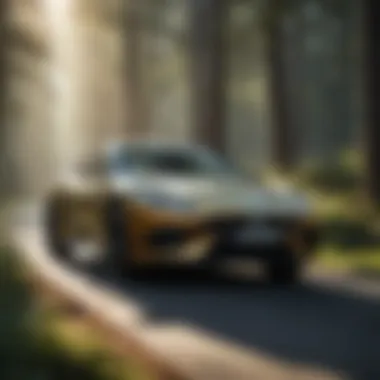
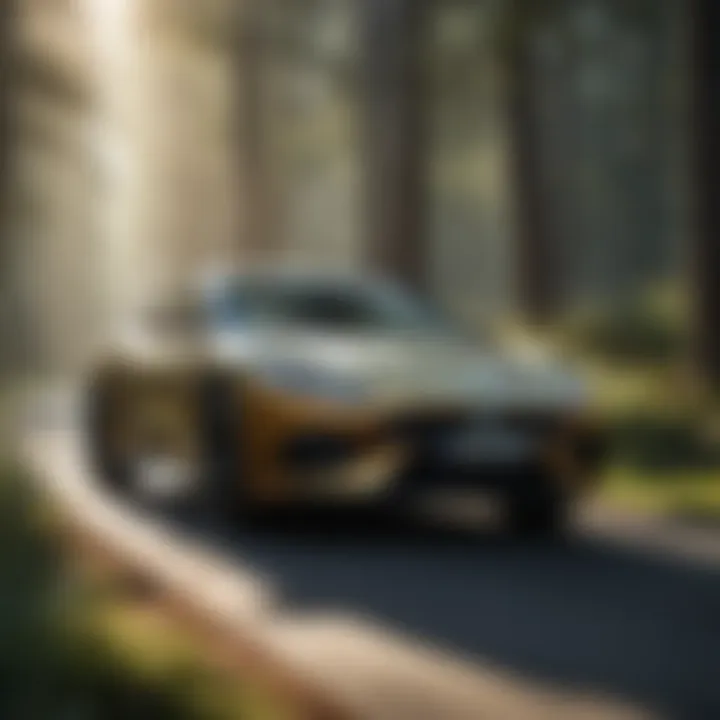
Molding
Molding in SMC preparation refers to the shaping and compacting of the mixed compound into a preliminary form before it undergoes final compression molding. This stage determines the initial geometry and thickness of the SMC sheet, providing a foundation for subsequent processing steps. The key characteristic of molding in SMC preparation lies in its ability to facilitate the initial consolidation of the composite mixture, setting the stage for further densification and shaping in the compression molding phase. Effective molding ensures proper alignment of reinforcement fibers and resin distribution, optimizing the material's structural performance and surface finish. However, challenges such as material flow control and tooling complexity can arise during the molding process, necessitating careful design considerations and process optimization to achieve consistent SMC sheets.
Stabilizing
Stabilizing serves as a critical step post-mixing in SMC preparation, allowing the composite paste to achieve a stable consistency and cure readiness before further processing. The key characteristic of stabilizing is its role in enhancing the self-supporting properties of the SMC mixture, enabling it to maintain shape and structure without deformation during transportation and storage. Stabilizing promotes uniform curing and dimensional stability in the composite, ensuring minimal distortion and defects in the final part. While stabilizing contributes to material handling efficiency and process control, prolonged stabilization times or inadequately stabilized compounds can lead to variations in mechanical properties and surface quality, underscoring the importance of optimized stabilization practices in SMC manufacturing.
Properties of Sheet Molding Composite
In the realm of sheet molding composite (SMC), understanding the properties holds paramount importance. Properties dictate the performance, durability, and applicability of SMC in various industries. This section serves as a detailed exploration of the mechanical, thermal, and electrical aspects of SMC, shedding light on its exceptional characteristics that set it apart in modern engineering and design.
Mechanical Properties
Tensile Strength
Tensile strength is a critical mechanical property of SMC, representing its ability to withstand tension before breaking. The high tensile strength of SMC makes it a preferred choice for applications requiring robust structural integrity. Its unique feature lies in its capacity to maintain shape and resist deformation under significant force, ensuring reliability in demanding environments. The advantages of high tensile strength in SMC translate to enhanced performance and longevity, making it a popular material for structural components that undergo substantial stress.
Flexural Strength
Flexural strength is another key mechanical property of SMC, determining its resistance to bending forces. The exceptional flexural strength of SMC enables it to withstand bending without fracturing, adding to its structural durability. The unique feature of flexural strength lies in its ability to distribute stress evenly, minimizing the risk of structural failure. Incorporating SMC with high flexural strength offers reliability and stability in applications where bending forces are prevalent.
Impact Resistance
Impact resistance is a critical mechanical property that evaluates SMC's ability to absorb sudden shocks without breaking. The remarkable impact resistance of SMC ensures protection against external impacts, enhancing its durability in rugged environments. The unique feature of impact resistance lies in its capacity to dissipate energy upon impact, preventing structural damage. By exhibiting superior impact resistance, SMC proves to be a reliable choice for applications subjected to impact and collision scenarios.
Thermal Properties
Heat Deflection Temperature
Heat deflection temperature is a vital thermal property of SMC, indicating its ability to withstand elevated temperatures without deforming. The high heat deflection temperature of SMC makes it a suitable option for applications exposed to thermal stresses, ensuring dimensional stability under heat. Its unique feature lies in maintaining rigidity and shape integrity at elevated temperatures, offering reliability in high-temperature environments. Leveraging SMC with high heat deflection temperature enhances its performance and longevity in thermal applications.
Thermal Conductivity
Thermal conductivity is a crucial thermal property that determines SMC's ability to conduct heat efficiently. The optimal thermal conductivity of SMC facilitates heat transfer across its structure, contributing to thermal management in various applications. The unique feature of thermal conductivity lies in its capacity to regulate temperature gradients, ensuring consistent heat distribution. By incorporating SMC with high thermal conductivity, heat dissipation and thermal efficiency are enhanced in heat-sensitive environments.
Coefficient of Thermal Expansion
The coefficient of thermal expansion is a significant thermal property that reflects SMC's dimensional response to temperature variations. The low coefficient of thermal expansion of SMC indicates minimal dimensional changes with temperature fluctuations, ensuring dimensional stability. Its unique feature lies in maintaining structural integrity and avoiding warping or distortion due to thermal expansion, guaranteeing reliability in fluctuating temperature conditions. Harnessing SMC with a low coefficient of thermal expansion ensures dimensional accuracy and consistency in temperature-sensitive applications.
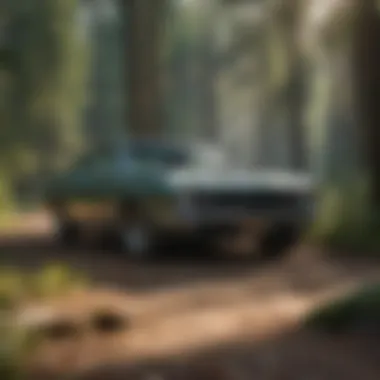
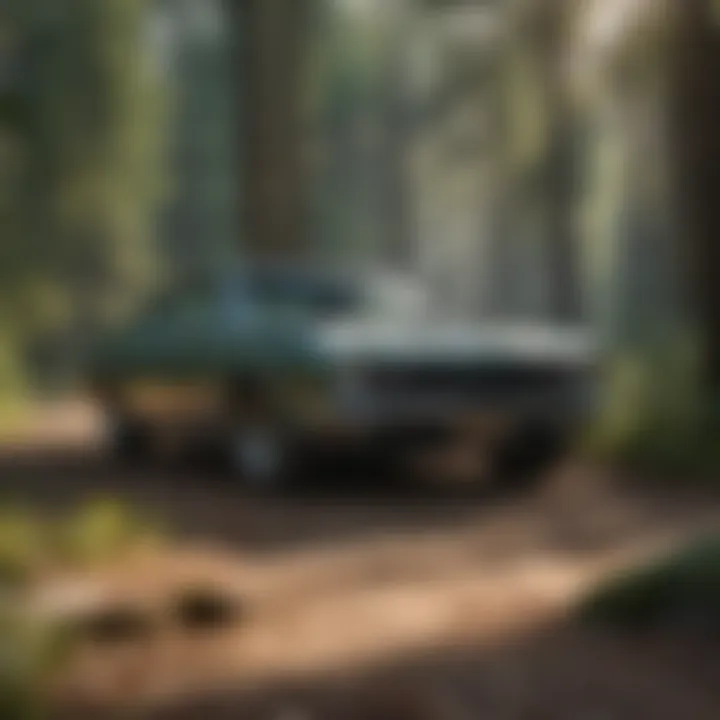
Electrical Properties
Dielectric Strength
Dielectric strength is a critical electrical property of SMC, illustrating its capacity to resist electrical breakdown under voltage stress. The high dielectric strength of SMC ensures insulation integrity and protection against electrical failures, enhancing its reliability in electrical applications. The unique feature of dielectric strength lies in its ability to withstand high voltages without conducting electricity, ensuring safety and efficiency. By incorporating SMC with high dielectric strength, electrical insulation and performance are optimized in diverse electrical systems.
Volume Resistivity
Volume resistivity is an essential electrical property that characterizes SMC's resistance to electrical current flow. The high volume resistivity of SMC signifies its insulating capability and impedance to electrical conduction, maintaining electrical integrity. The unique feature of volume resistivity lies in its ability to control current flow and prevent electrical leakage, ensuring stability in electrical circuits. Utilizing SMC with high volume resistivity enhances electrical insulation and reliability in applications requiring controlled conductivity.
Arc Resistance
Arc resistance is a crucial electrical property that demonstrates SMC's ability to resist arc formation and tracking under high voltage conditions. The exceptional arc resistance of SMC prevents arc propagation and tracking, safeguarding against electrical breakdowns and fires. Its unique feature lies in extinguishing arcs and preventing electrical faults, ensuring operational safety in high-voltage environments. Incorporating SMC with high arc resistance enhances electrical safety and reliability in critical electrical systems.
Environmental Impact and Sustainability
In a world increasingly focused on environmental conservation and sustainable practices, addressing the environmental impact and sustainability of materials like Sheet Molding Composite (SMC) is crucial. This section within the broader article serves as a nuanced exploration of how SMC intersects with pressing environmental concerns. It highlights the specific elements, benefits, and considerations of environmental impact and sustainability in the context of SMC, catering to a discerning audience of forestry professionals and academics seeking comprehensive insights.
Recyclability of SMC
Challenges
Delving into the challenges surrounding the recyclability of SMC unveils a complex landscape. The process of recycling SMC poses particular obstacles due to its composite nature, combining various materials like resin, reinforcements, and fillers. Disassembling these components in a way that maintains their integrity and allows for effective reprocessing presents a unique challenge. Despite these complexities, advancements in recycling technologies continue to push the boundaries of what is possible in the realm of SMC recyclability, making it a focal point in sustainable material practices. Understanding these challenges is essential in grasping the full scope of SMC's environmental footprint and the efforts required to enhance its recyclability.
Innovations
The realm of innovations in SMC recyclability showcases promising developments that have the potential to revolutionize the way SMC is reused and repurposed. From novel recycling methods to alternative uses for recycled SMC materials, innovation is at the forefront of sustainable material practices. These innovations not only address current challenges but also open up new possibilities for the circular economy, where SMC waste can be effectively reintegrated into production processes. Embracing these innovations is key to driving sustainability within the SMC industry and maximizing the environmental benefits of this versatile material.
Future Prospects
Looking ahead, the future prospects of SMC recyclability hold considerable promise for advancing environmental sustainability goals. With ongoing research and development efforts focused on enhancing the recyclability of SMC, the horizon looks optimistic. Anticipated improvements in recycling efficiency, coupled with a growing emphasis on sustainable material sourcing, position SMC as a frontrunner in eco-friendly engineering solutions. The future prospects of SMC recyclability are not just theoretical aspirations but concrete goals driving real-world change towards a greener, more sustainable industrial landscape.
Sustainable Practices in SMC Manufacturing
Material Sourcing
The fundamental step of material sourcing in SMC manufacturing sets the tone for the environmental impact of the final product. Opting for sustainable and responsibly sourced raw materials is paramount in aligning SMC production with eco-friendly practices. From selecting recycled inputs to ensuring ethical sourcing practices, material sourcing holds the key to reducing the ecological footprint of SMC. By shedding light on the intricate details of material origins and tracing supply chain transparency, this section underscores the critical role of material sourcing in fostering sustainability within the SMC industry.
Energy Efficiency
Efficient energy utilization throughout the manufacturing process is a cornerstone of sustainable practices in SMC production. Minimizing energy waste, adopting renewable energy sources, and optimizing operational processes contribute to reducing the carbon footprint associated with SMC manufacturing. Embracing energy-efficient practices not only aligns SMC production with environmental objectives but also presents economic benefits through lower operational costs and heightened resource efficiency. Exploring the nuances of energy efficiency in SMC manufacturing unveils the interconnected relationship between environmental stewardship and industrial innovation.
Waste Reduction
The imperative to minimize waste generation in SMC manufacturing underscores a holistic approach to sustainability. Implementing waste reduction strategies, such as recycling production leftovers and optimizing material usage, fosters a closed-loop system that mitigates environmental harm. By delving into the mechanisms of waste reduction within SMC manufacturing, this section elucidates the practical implications of circular economy principles. Incorporating waste reduction measures not only bolsters the environmental credentials of SMC but also cultivates a culture of environmental responsibility within the industry, heralding a new era of sustainable manufacturing practices.