In-Depth Exploration of Delamination Testing Procedures and Significance
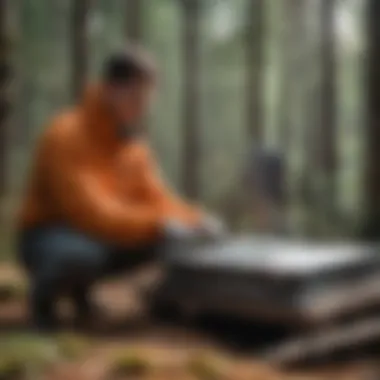
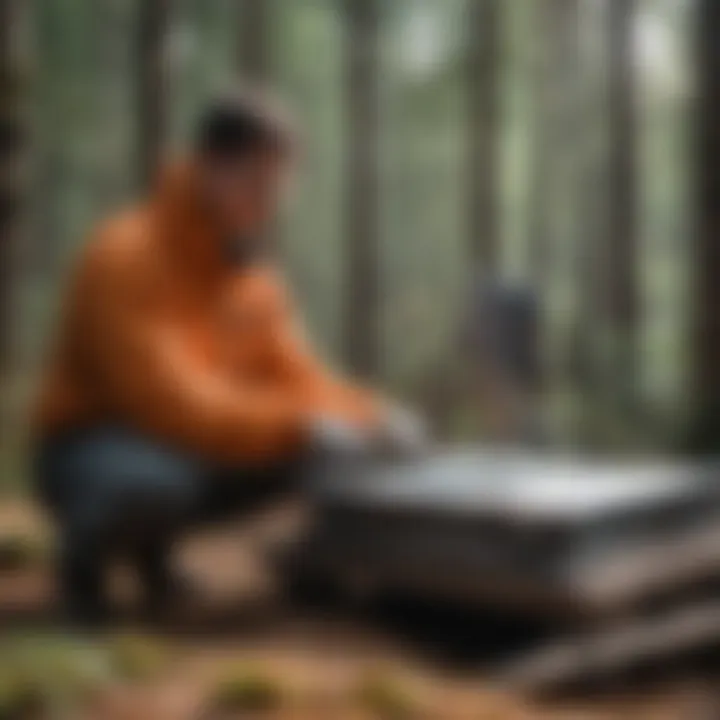
Management and Preservation of Evergreen Forests
Reflecting on the historical significance of American evergreen forests and native practices provides valuable insights into conservation practices and sustainable management approaches. Understanding the intricate balance between preservation efforts and utilization of resources is essential for maintaining the ecological health of these vital ecosystems. The latest research studies on evergreen forests offer compelling data on biodiversity trends, forest regeneration, and adaptive strategies to mitigate environmental impacts. Through showcasing ongoing initiatives that protect and enhance American evergreen landscapes, success stories emerge, demonstrating the positive outcomes achievable through dedicated conservation efforts.
Introduction
In the realm of materials testing, delamination tests stand as a fundamental pillar in ensuring the structural integrity and quality of composite materials. This comprehensive guide aims to delve deep into the intricate world of delamination testing, shedding light on its significance, methodologies, and real-world applications across industries. Understanding delamination tests is paramount for industries such as aerospace, manufacturing, and construction to evaluate the durability and reliability of composite materials used in various applications.
Within this article, we will explore the essence of delamination tests, offering a detailed overview that encompasses the core principles, processes, and implications of conducting such tests. As we delve into this subject, readers will gain a profound insight into the critical role that delamination testing plays in upholding the standards of quality control within different sectors.
Overview of Delamination Tests
Delamination tests serve as a crucial technique for evaluating the bonding strength and integrity of composite materials. In essence, delamination refers to the separation of layers within a composite structure, which can significantly compromise its structural stability and performance. Therefore, the precise identification and assessment of delamination through testing procedures are essential for ensuring the structural soundness and reliability of composite materials.
One of the primary objectives of delamination testing is to detect potential defects or weak points within a composite structure that may lead to catastrophic failures under operational conditions. By subjecting composite samples to various testing methods such as peel tests, shear tests, and compression tests, researchers can accurately assess the adhesion strength between material layers and detect any signs of delamination.
Moreover, understanding the underlying factors and mechanisms that contribute to delamination is vital for developing effective preventive measures and quality control protocols. Delamination tests provide valuable insights into the performance characteristics and durability of composite materials, enabling manufacturers and engineers to make informed decisions regarding material selection, design optimization, and structural integrity.
By examining the nuances of delamination tests and their practical implications, this section aims to equip readers with a comprehensive understanding of the importance and relevance of delamination testing within the realm of materials science and engineering.
Significance of Delamination Tests
Delamination tests hold a pivotal role in the evaluation and verification of composite materials' structural integrity and durability. Within the context of this article, the significance of delamination tests illuminates the critical nature of ensuring the quality and reliability of these materials in various industries such as manufacturing, construction, and aerospace. The process of delamination testing serves as a fundamental quality control measure, aiming to identify any potential weaknesses or flaws that could jeopardize the final product's performance and longevity.
Delamination tests play a crucial role in guaranteeing that composite materials can withstand the rigorous demands imposed on them within their respective industries. By subjecting these materials to meticulous testing procedures, manufacturers can ascertain their capacity to endure external pressures, environmental factors, and operational stresses. The meticulous evaluation of delamination ensures that components fabricated from composite materials possess the necessary strength and durability to fulfill their intended functions without compromising safety or efficiency.
Moreover, the significance of delamination tests extends beyond mere material inspection. These tests act as a safeguard against potential disasters or malfunctions that could result from undetected flaws within composite structures. By emphasizing the importance of preemptive testing, industries can preemptively address any structural weaknesses or vulnerabilities, thereby averting costly repairs, product recalls, or, even worse, catastrophic accidents.
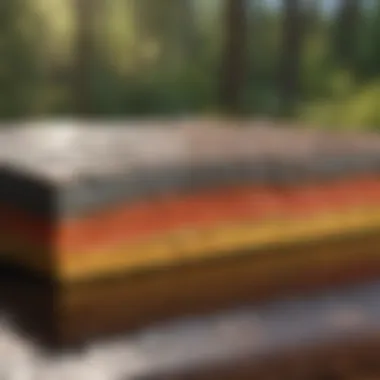
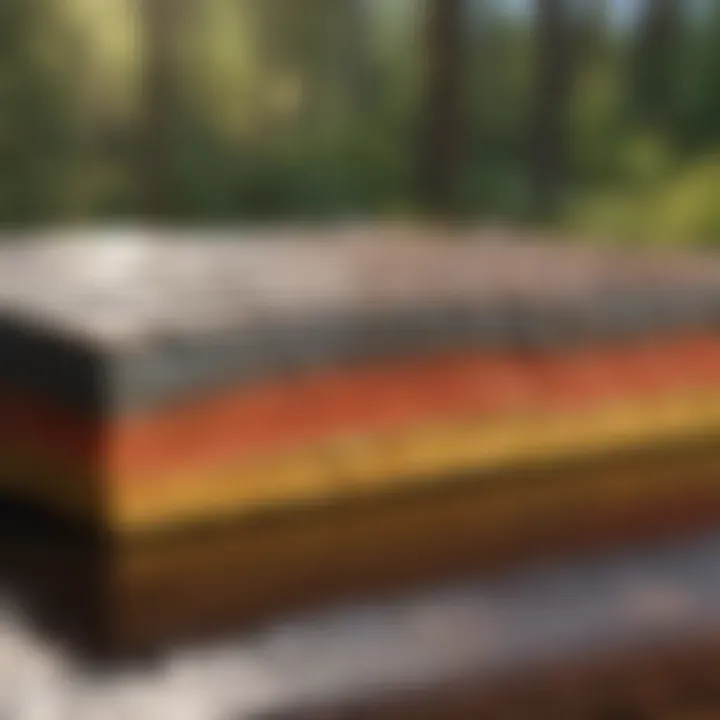
In essence, delamination tests stand as a cornerstone of quality assurance, underpinning the reliability and performance of composite materials in diverse industrial sectors. Through meticulous examination and analysis, delamination tests facilitate the creation and utilization of composite products that meet stringent quality standards, ensuring optimal performance, longevity, and safety.
Ensuring Structural Integrity
Ensuring structural integrity through delamination tests involves a comprehensive process aimed at verifying the robustness and stability of composite materials. The primary goal of assessing structural integrity is to confirm that the materials exhibit the required strength, cohesion, and resilience to withstand operational loads and environmental factors.
One crucial aspect of testing structural integrity is the identification of potential weak points or areas susceptible to delamination. By pinpointing these vulnerable spots early on, manufacturers and engineers can implement targeted reinforcement strategies to fortify the material and mitigate the risk of failure.
Furthermore, ensuring structural integrity through delamination tests allows for the optimization of material design and manufacturing processes. By uncovering insights into how composite materials behave under stress and strain, industries can refine their production techniques to enhance product performance and longevity.
Overall, focusing on ensuring structural integrity via delamination testing is essential for upholding quality standards, enhancing product reliability, and minimizing the risk of material failure in critical applications.
Methods of Delamination Testing
Delamination testing is a crucial process in assessing the integrity and durability of composite materials, making it a pivotal aspect of quality control in various industries such as manufacturing, construction, and aerospace. Understanding the different methods of delamination testing is essential for ensuring that materials meet specified standards and are safe for use in diverse applications. By focusing on specific elements within the realm of delamination testing, professionals can identify defects, weakness, or potential failures in composite structures before they escalate into larger issues.
Peel Test Method
The peel test method is a widely used approach in delamination testing that involves applying a gradually increasing force to separate two bonded layers. By measuring the force required to peel the layers apart, technicians can assess the adhesion strength and detect any weaknesses or imperfections in the bonding interface. This method is particularly effective in evaluating the bond quality between composite layers and highlighting potential delamination issues that may arise under varying stress conditions.
Shear Test Method
Another common technique in delamination testing is the shear test method, which evaluates the interfacial strength between bonded materials by applying a lateral force that causes one layer to slide relative to the other. This method assesses the structural stability of composite materials under shear stress, helping to determine their resistance to lateral displacement and potential delamination. Professionals utilize the shear test method to identify areas of weakness or inadequate bonding that could compromise the overall integrity of the material.
Compression Test Method
The compression test method involves subjecting a sample to compressive forces to assess its resistance to crushing or collapsing. By analyzing how the material withstands compression, technicians can evaluate its structural robustness and susceptibility to delamination under pressure. This method provides insights into the material's compressive strength and its ability to maintain structural integrity without developing delamination defects. Engaging in comprehensive compression testing is crucial for ensuring that composite materials can withstand external loads effectively.
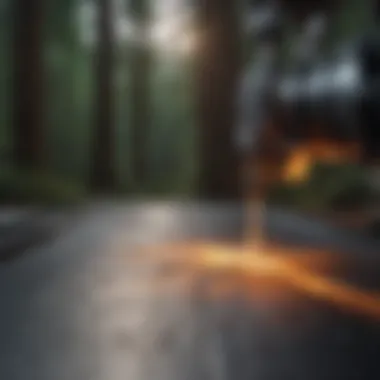
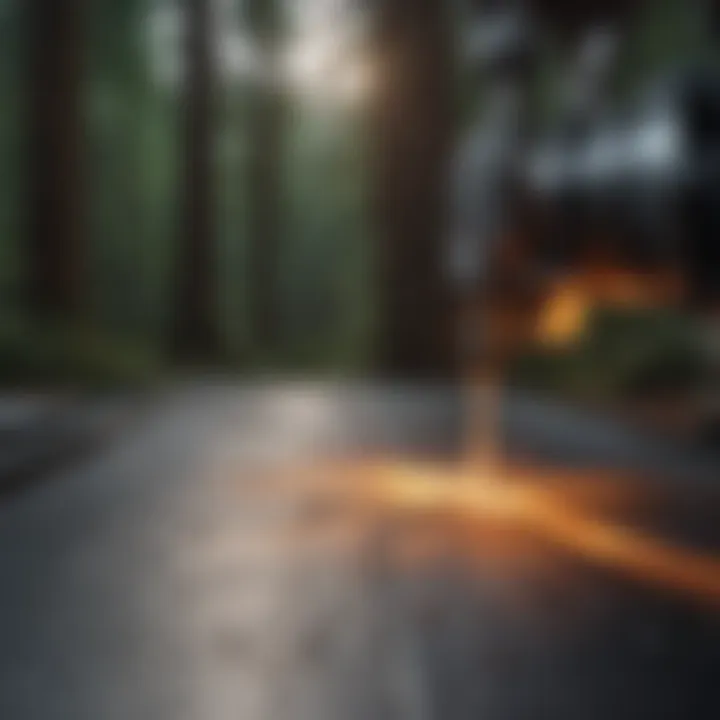
Common Industries Utilizing Delamination Tests
Delamination tests hold a significant position in various industries due to their crucial role in assessing the durability and integrity of composite materials. The application of delamination tests is especially prevalent in industries such as manufacturing, construction, and aerospace, where the quality control of composite materials is paramount. These tests ensure that the structural components meet the required standards for strength and reliability in demanding operational conditions.
Aerospace Industry
The aerospace industry stands out as a key sector that extensively utilizes delamination tests to evaluate the structural integrity of advanced composite materials used in aircraft and spacecraft manufacturing. Given the stringent safety and performance requirements in aerospace applications, the accurate detection and assessment of delamination are vital to prevent potential structural failures. Aerospace engineers rely on delamination tests to identify any separation or weak bonding between composite layers that could compromise the overall strength of the aircraft components.
Mainly in the aircraft's critical components like wings, fuselage, and tail sections, delamination testing plays a crucial role in ensuring the structural soundness and compliance with stringent industry regulations. Through advanced techniques like acoustic emission testing, aerospace professionals can detect and monitor any potential delamination issues, allowing for timely intervention and maintenance to prevent catastrophic failures during flight operations.
The aerospace industry's adoption of delamination tests underscores the commitment to employing cutting-edge technologies and methodologies to enhance the safety and durability of aircraft structures. By systematically conducting delamination tests as part of the quality control process, aerospace manufacturers can mitigate risks associated with material delamination and uphold the highest standards of performance and reliability in the aviation sector.
Challenges in Delamination Testing
Delamination testing is a critical aspect of quality control in various industries, including manufacturing, construction, and aerospace. Understanding the challenges associated with delamination testing is paramount for ensuring the integrity and reliability of composite materials. One of the key challenges in delamination testing is the detection of micro-delamination. Micro-delamination refers to the separation of layers at a microscopic level, which can be difficult to identify using traditional testing methods. Detecting micro-delamination requires high precision and advanced techniques to ensure the accurate assessment of material integrity.
Furthermore, another significant challenge in delamination testing is the analysis of environmental factors that contribute to delamination. Environmental conditions such as temperature fluctuations, moisture exposure, and chemical interactions can accelerate delamination processes. Addressing these environmental challenges involves implementing preventive measures, such as proper storage conditions and material handling practices, to mitigate potential delamination risks.
Moreover, the complexity of composite structures poses a challenge in delamination testing, as different materials and bonding techniques can impact delamination susceptibility. Understanding the interplay between material properties and structural design is essential for effectively conducting delamination tests and interpreting test results. This challenge underscores the importance of employing experienced professionals and utilizing state-of-the-art equipment to ensure the accuracy and reliability of delamination testing outcomes.
Factors Affecting Delamination
In the realm of delamination testing, understanding the factors that can influence this phenomenon is crucial to ensuring the structural integrity of composite materials. Factors affecting delamination encompass a wide array of elements that can impact the bonding and cohesion within composite structures. These elements include but are not limited to material properties, manufacturing processes, environmental conditions, and operational stresses. By examining these factors in detail, manufacturers and engineers can preemptively address potential issues and optimize the durability and reliability of composite materials.
Factors affecting delamination have direct implications on the overall quality and longevity of composite structures. The material properties such as adhesive strength, interfacial bonding, and resin distribution play a significant role in determining the susceptibility of a material to delamination. Additionally, the manufacturing processes employed, such as curing temperatures, pressures, and cooling rates, can influence the internal stresses and bonding quality within the composite. Moreover, environmental factors like temperature fluctuations, moisture absorption, and exposure to harsh chemicals can accelerate delamination processes, compromising the structural integrity of the material.
Addressing factors affecting delamination requires a comprehensive approach that considers each variable's potential impact on the composite material's performance. Careful consideration of material selection, manufacturing procedures, and environmental conditions is essential to mitigate delamination risks effectively. By proactively identifying and managing these factors, manufacturers can enhance the overall quality and reliability of composite materials, reducing the likelihood of delamination-related failures in critical applications.
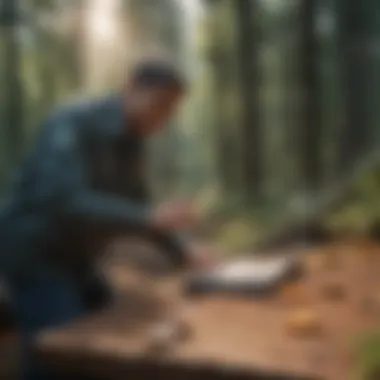
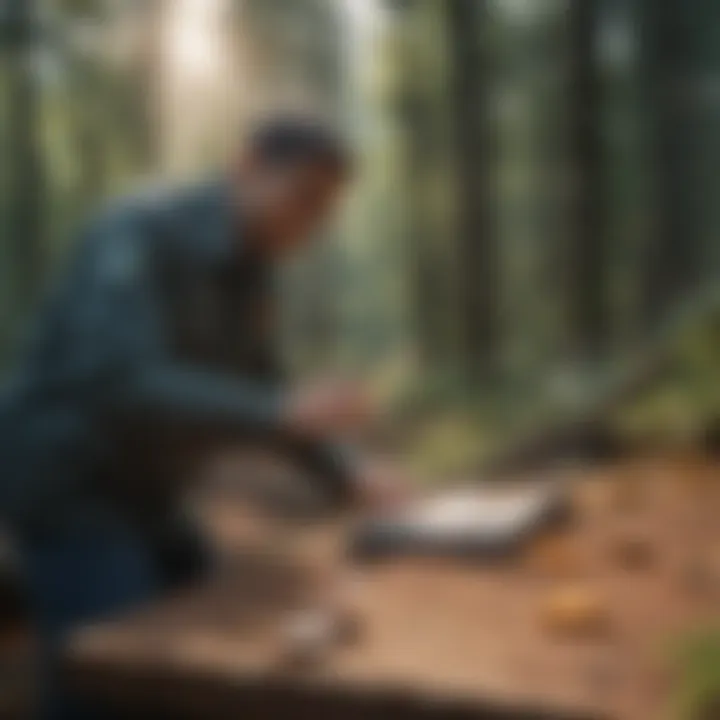
Preventive Measures for Delamination: Enhancing Durability
In the realm of delamination testing, preventive measures hold a paramount significance in ensuring the durability and longevity of composite materials. This section focuses on elucidating the pivotal role of preventive measures in mitigating delamination risks and enhancing structural integrity. By implementing proactive strategies, manufacturers and industry professionals can proactively address potential delamination issues, thereby upholding the quality standards of their products. Preventive measures serve as a preemptive approach to minimizing the occurrence of delamination, ultimately bolstering the reliability and performance of composite materials.
Proper Bonding Techniques: The Foundation of Delamination Prevention
Proper bonding techniques constitute the cornerstone of delamination prevention, offering a comprehensive solution to fortify the bond strength between composite layers. This subsection delves into the intricacies of selecting the appropriate adhesive materials, surface preparation methods, and bonding parameters to ensure optimal adhesion and cohesion within composite structures. Emphasizing the importance of meticulous bonding processes, this section underscores the significance of adhering to industry best practices and standards to minimize the risk of delamination.
Ensuring a robust bond interface is essential in averting delamination failures, as any inadequacies in bonding can compromise the structural integrity of composite components. With a focus on precision and accuracy, proper bonding techniques involve meticulous surface treatments, adhesive application methods, and curing processes to enhance interfacial adhesion and prevent delamination propagation. By adhering to established bonding protocols and quality control measures, manufacturers can fortify the bond line strength, effectively reducing the susceptibility to delamination under mechanical or environmental stressors.
Advanced Techniques in Delamination Testing
In the realm of delamination testing, the utilization of advanced techniques holds paramount significance. These cutting-edge methods enhance the precision and efficiency of assessing composite materials, thereby ensuring utmost reliability in structural integrity evaluations. One of the key benefits of incorporating advanced techniques is the ability to detect delamination at microscopic levels, offering a deeper insight into potential flaws that conventional methods might overlook. By exploring advanced techniques, such as non-destructive testing methods, thermal imaging, and acoustic emission testing, manufacturers and researchers can elevate the quality control standards to unprecedented levels. It is important to note that advanced techniques require specialized equipment and trained professionals to execute the tests accurately and derive meaningful conclusions.
Acoustic Emission Testing
Acoustic emission testing, a pivotal subset of advanced delamination testing techniques, presents a revolutionary approach to detecting and monitoring the progression of delamination within composite materials. This method involves capturing the transient stress waves produced during the initiation and propagation of delamination, providing valuable insights into the structural health and durability of the material being tested. The key advantage of acoustic emission testing lies in its non-intrusive nature, allowing real-time monitoring of structural defects without causing further damage to the specimen. Furthermore, the ability to distinguish different sources of acoustic emissions enables precise localization of delamination areas, aiding in targeted repairs and preventive measures. Engineers and researchers rely on acoustic emission testing to identify hidden delamination, assess the extent of damage, and ultimately enhance the overall quality and longevity of composite structures.
Conclusion
In this final section, we encapsulate the pivotal role of the Conclusion within the broader context of the article on Delamination Testing. The Conclusion serves as a crucial component that distills the essence of the discussions, insights, and findings unearthed throughout this comprehensive guide. It acts as the summarizing force that reinforces the significance of delamination tests in evaluating the structural integrity and durability of composite materials across various industries.
One of the primary considerations of the Conclusion is its ability to harmonize the intricate layers of information presented in preceding sections, offering a cohesive narrative that resonates with both seasoned professionals and aspiring academics in the field of materials science. By outlining the key takeaways and implications from the in-depth exploration of delamination testing methods, challenges, and preventive measures, the Conclusion elevates the discourse to a reflective plane, urging readers to internalize the salient points and translate them into actionable insights within their respective domains.
Moreover, the Conclusion serves as a compass that steers the reader towards a definitive understanding of the critical role played by delamination tests in maintaining quality assurance and compliance standards in industries such as aerospace, manufacturing, and construction. It underscores the ongoing evolution and innovation within delamination testing techniques, underscoring the need for continuous learning and adaptation to emerging trends and technologies that shape the landscape of materials evaluation and quality control.
By weaving together the threads of knowledge, analysis, and practical implications, the Conclusion acts as a beacon of enlightenment, shedding light on the nuanced dynamics of delamination testing and emphasizing its enduring relevance in a rapidly evolving industrial milieu.
Key Takeaways
As we distill the core insights and overarching themes embedded in this comprehensive guide to Delamination Testing, several key takeaways emerge that encapsulate the essence of the discourse:
- Importance of Quality Assurance: The fundamental role of delamination tests in upholding quality standards and ensuring structural integrity across diverse industries underscores the significance of robust testing protocols and methodologies.
- Innovative Testing Techniques: The evolution of advanced methods such as Acoustic Emission Testing signifies a paradigm shift towards more precise and time-efficient assessment approaches, reflecting the industry's commitment to embracing technological advancements.
- Challenges and Solutions: The detection of micro-delamination poses a significant challenge that necessitates proactive preventive measures and meticulous attention to environmental factors to mitigate potential risks and enhance testing accuracy.
- Holistic Approach to Delamination Testing: By combining traditional testing methods like Peel, Shear, and Compression tests with cutting-edge solutions, industries can adopt a holistic approach that balances legacy practices with contemporary trends to achieve comprehensive and reliable testing outcomes.
- Continuous Learning and Adaptation: The Conclusion reinforces the imperative for professionals and academics to engage in ongoing learning and stay abreast of emerging trends, technological advancements, and regulatory changes shaping the landscape of delamination testing.
Through these key takeaways, readers are equipped with a nuanced understanding that empowers them to navigate the complexities of delamination testing with acumen and proficiency, fostering a culture of excellence and innovation within the realm of materials science.